The Best Strategy To Use For Volution Bearing
The Best Strategy To Use For Volution Bearing
Blog Article
5 Easy Facts About Volution Bearing Described
Table of Contents7 Easy Facts About Volution Bearing ShownGetting The Volution Bearing To WorkVolution Bearing for DummiesThe Buzz on Volution Bearing
This is the amount of time that a group of obviously the same bearings will finish or go beyond prior to the formation of a tiredness spall.This computation can be somewhat made complex as it relies on the loved one magnitudes of the radial and drive loads per other and the call angle created by the bearing. It would certainly be as well difficult to reveal all the approaches of determining P for all the bearing types revealed. For conical roller bearings, the "K" drive aspect is employed.
Radial cylindrical roller bearings that have opposing flanges on their inner and external races have a limited capability of taking a drive load though the size of the rollers. It is so restricted that we do not suggest customers deliberately do this. Acceptable thrust loading is using roller ends and flanges for recurring thrust and locating objectives.
Lots of applications do not run at a constant tons or rate, and to select bearings for a specific score life in hours based upon the most awful operating problem might prove wasteful (https://www.storeboard.com/volutionbearing). Usually, a responsibility cycle can be defined for the numerous operating conditions (load and rate) and the portion of time at each
Little Known Questions About Volution Bearing.
In such circumstances, a complete obligation cycle occurs within one transformation of the bearing. Moreover, the two examples can be combined for numerous expected operating problems with reciprocating activity and various peak loads and rates. Determining the ranking life when tons and rates differ entails first determining the L10 ranking life at each running problem of the responsibility cycle.
T1, T2, Tn = portion of time at various conditions, shared as a decimal T1 + T2 + Tn = 1 Lp1, Lp2, Lpn = Life in hours for each period of continuous tons and rate When a bearing does not make a complete rotation however oscillates to and fro in operation, a lower equal radial tons can be calculated using the formula listed below: Pe = Po x (/ 90)1/e where: Pe = equal dynamic radial load Po = real oscillating radial tons = angle of oscillation, in degrees e = 10/3 (Roller Bearings) 3.0(Round Brgs) Some applications produce extremely high radial and thrust lots, and it may not be literally possible or viable to utilize a solitary bearing that can taking both sorts of tons.
When this occurs, the equipment developer have to take care to make certain that the radial bearing takes just the radial load, and the drive bearing takes just the thrust lots. An excellent way to complete this is to make use of a cylindrical roller bearing with one straight race at the "radial" location, as this bearing can not take any drive.
One means to complete this is to make the fit of the outer races very loose in their housings: commonly.5 mm/.020 In. to 1.0 mm/.040 In. Life modification factors enable the initial equipment supplier to far better anticipate the actual life span and integrity of bearings that you select and set up in your devices.
Things about Volution Bearing
Life modification variables, a1, a2 and a3, can theoretically be higher or much less than 1. manufacturer athens ga.0, depending upon their evaluation. In the OEM's procedure of forecasting the solution dependability of his/her devices, it is in some cases required look here to increase the integrity of the picked bearings to forecast a much longer imply time between failures
If a reduced value for L10 is calculated with an a1 factor, and it is not acceptable, then a bearing with better Dynamic Ability requires to be chosen. Integrity - % Ln a1 element 90 L10 1.00 95 L5 0.64 96L4 0.55 97 L6 0.47 98 L2 0.37 99 L1 0.25 There have been numerous renovations in birthing design and manufacture for many years that have been proven in life examinations that result in boosted L10 rating life.
Lots of bearing applications are much from laboratory conditions. Therefore it can be hard to warrant an a3 aspect higher than 1.0. Conditions such as high temperature level, contamination, outside vibration, and so on will lead to an a3 element less than 1. If the lubrication is exceptional and the running rate high enough, a dramatically boosted lube film can create in between the bearing's interior call surface areas warranting an a3 aspect more than 1.0.
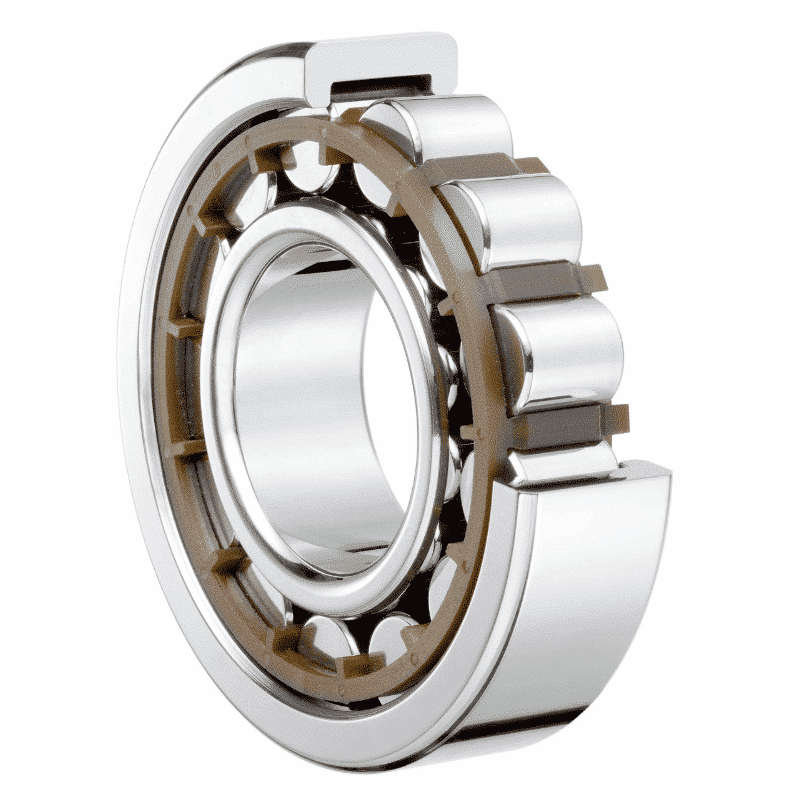
The 9-Minute Rule for Volution Bearing
The following formula is utilized to compute the System Rating Life: L10sys = (L1-w + L2-w + Ln-w)-1/ w where L10sys = score life for the system of bearings L1, L2, Ln = rating life for the individual bearings in the system w = 10/9 for ball bearings and w = 9/8 for roller bearings It has been learned from experience that bearings call for a minimal applied lots to guarantee grip for the moving aspects so they roll as the shaft begins to revolve. https://volution-bearing-46080167.hubspotpagebuilder.com/blog/volution-bearing-revolutionizing-bearings-for-extreme-environments.
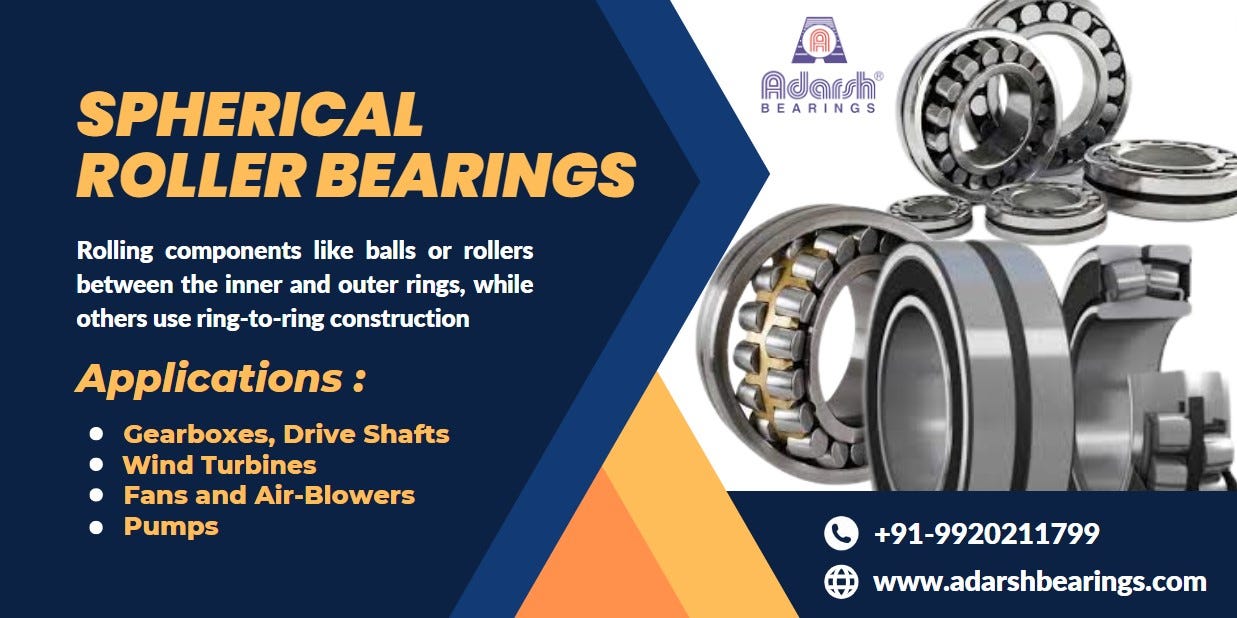
Report this page